February 2018
Consulting Technical Service Visit
A major seating supplier to a Global JOEM requested a Technical Service visit for support to reduce high sCrap and Repair rates and other foam related defects on one of their two Race Track (RT) production lines. The RT line has xx* carriers with two seating tools on each individual carrier.
The customer purchased 4 fully formulated polyol blends and a TM Blended isocyanate, which are regularly provided to the plant in bulk. A Cannon 5 stream HP head is used to robotically dispense the mixed, liquid, PU chemicals into the two seating tools with an approximate time of the pour lid close time takes xx* seconds.
The number one foam defect, which was the major contributor to high sCrap and Repair on RT Line 1, was isolated to one type of Front Seat Back for one vehicle model. The root cause for the foam defect was difficult to identify due to the complexity of the foam structure around the foam defect.
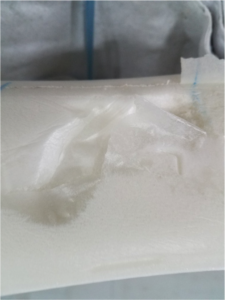
sCrap Seat Void
Consulting Technical Service Timeline
The first shift on Monday was utilized to better understand the set up and operation of Line 1 Racetrack line. We identified and prioritized the foam defects that were commonly noticed during production. Collecting samples of each type of foam related to the defect, greatly expedited the root cause analysis/prioritization of our work on the RT line.
The main cause for sCrap on this line was a foam defect in the air bag region of the front seat back, which had certain areas that required void free foam. Voids in this area were difficult to identify as they were either collapse voids due to leakage or post gel point pressure relief voids.
Tuesday and Wednesday were used for improved sealing of the tools as well as ratio, shot times, and pour pattern adjustments to confirm the type of void in this region of the cushions. Countermeasures were employed on this particular line to confirm that the foam defect was in fact due to collapse voids.
Through these testing efforts, it was discovered that there was a leakage along a seal of the upper back, side edge, of the seat as the major root cause. To correct the issue sealing tape was used to correct the seal and to control venting. The correction to the seal greatly reduced the defect rate.
To further optimize the pour pattern, ratio and shot weights were added into these specific front seat back cushions.
By Friday the defect rate in the air bag region of these seats was reduced by over 90%.
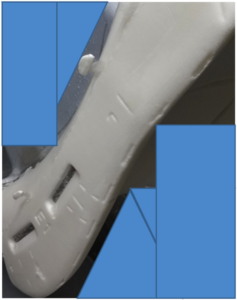
Void Free Seat Back
Root Cause Analysis – Results
The rate of collapse voids for sCrap/Repair in the air bag region of the front seat back cushions was reduced by 90% by Friday. This repair resulted in a savings of over $1,000 per day in scrap.
The countermeasures applied to this one model front seat back was also applied to additional front seat back cushions on this and the other RT line for additional cost savings. In addition, due to the improved productivity from the reduction in sCrap and Repair rates, the overtime hours were reduced by over two hours per day. Providing the company with an additional labor cost savings of over $1,500 per day.
Overall, the combined cost reductions have been consistent and combined for a savings of over $2,000 per day.
A full detailed report was provided to the customer once final analysis and presentation of findings was complete.
*Some information has been removed to protect the intellectual property of our customer.